74” WIDE X .500” TO .040” THICK X 80,000# PRO-ECO/BUTECH/ASP EJECTOR HEAD SLITTING LINE (USED)
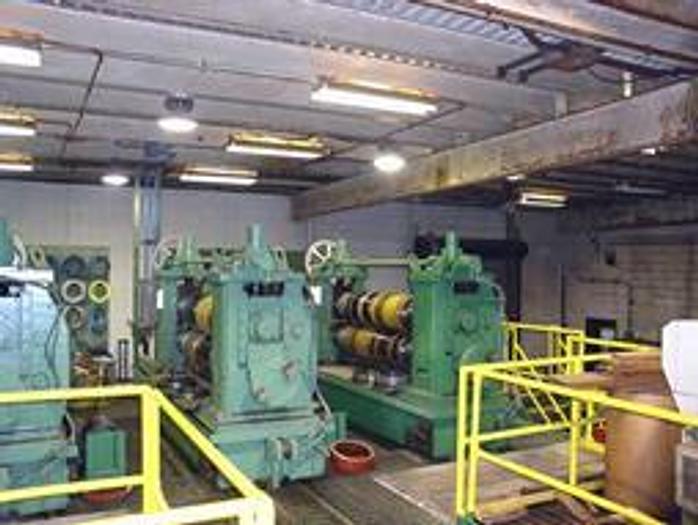
Specifications
Manufacturer | Pro-Eco/Butech |
Condition | Used |
Stock Number | VX-1664 |
Description
General Specifications:
Condition: Excellent w/Little Use (All mechanical has been checked.)
Year of Manufacture: Installed in Approximately 1995, Shutdown to be Re-Installed in 1999
Material: Stainless, Aluminum, High Strength Steel
Mode of Operation: Loop, Helper Drive, Pull Thru (Three Modes Possible)
Maximum Tensile Strength: 100,000 PSI
Maximum Shear Strength: 65,000 PSI
Maximum Yield Strength: 80,000 PSI
Maximum Width: 74"
Maximum Thickness: .500"
Thickness Range: .040" - .500"
Maximum Coil Weight at Uncoiler and Recoiler: 80,000#
Entry Coil ID at Uncoiler: 20" to 24"
Exit Coil ID at Recoiler: 20"
Entry Coil OD: 36" - 80"
Exit Coil OD: 36" - 80"
Line Speed (Full Torque): 150 FPM
Maximum Line Speed: 500 FPM
Maximum Slitting Capacity w/60,000 PSI Tensile: 4 Cuts of .500"
6 Cuts of .375"
8 Cuts of .250"
14 Cuts of .187"
16 Cuts of .135"
21 Cuts of .060"
Line Consists of the Following:
Pro-Eco Entry Floor Type Coil Car
- Mast/End Feed Type
- Floor Mounted
- Self-Contained Hydraulics
- Hydraulic Lift and Traverse
- Powered Positioning Rolls
Pro-Eco Double-End Cone Uncoiler
- Wichita High Tension Air Brake System on Both Cones
- Hydraulic Sliding Base w/Edge Control
- Feed-Up Drive w/Air Clutch
Fife or North American Automatic Edge Control
Pro-Eco 72" x .500" Heavy-Duty Peeler System
- Power Driven Hold Down Roll
- Hydraulic In/Out, Up/Down Travel
Pro-Eco 74" Roll Face Flattener Rolls
- Powered Entry Pinch Rolls
- Roller Bearings Throughout
- Alloy Hardened and Ground Rolls
- Adjustable Rolls to Set Flatness
- Motor Clutch System, Forward/Reverse
Butech 80" Entry Crop Shear
- Powered Entry Pinch Rolls
- Down-Cut Type
- Single Rake Blade
Pro-Eco Long Rotary Type Heavy-Duty Edge Guides
- Power Adjustment
- Individual Width Adjustment
- Large Multiple Roller Type on Each Individual Housing
Two (2) Pro-Eco Ejector Slitter Heads on Common Track Base
- (2)-10.5" Diameter Precision Arbors x 74" Effective Strip Width
- Set-Up Base for (2) Heads
- Powered Top Arbor Adjustment
- Powered Outboard Retraction
- Speeds from 0 to 150 FPM @ Full Slitting Capacity, 0 to 500 FPM Top Line Speed
- 150 HP, 0 to 500 V, 650 to 1,950 RPM DC Motor w/Drives and Controls
Cowles or Equivalent Tooling
- Full Complement of Knives, Spacers, & Rubber Strippers for 10.5" Arbors
- Full Complement of Tooling for (2) Separator Shafts
Design & Manufacture (2) New ASP .500" x 3" x 2,500# Hydraulic Scrap Winders (OPTIONAL)
- Ejector Type System
- Scrap Winder Receiving Containers for Automatic Dump System Using Crane
Build New Hydraulically Actuated Cross Over Pit Table
Pro-Eco 72" Tension Stand w/Separator Shaft
- Large Open Type for Threading
- Dragboard Type w/Heavy Fabric, Quick Side Change Boards
Pro-Eco Exit Pinch Rolls
Pro-Eco Recoiler Feed Table
- For Guiding Slit Strips into Recoiler Gripper Slot
24" ID Recoiler
- Hydraulic Pushoff
- Large Gripper Slot for ½" Thick Material
- Powered Snubber System
- 200 HP, 500 V DC Motor w/New Drive and Controls
- 74" Hydraulic Overarm Separator and Snubber w/(2) Shafts
Pro-Eco Exit Coil Car
- Self-Contained Hydraulics
- Hydraulic Lift and Traverse
(2) Pump & Tank Units w/Automatic Float Control
- (1) at Uncoiler Area & (1) at Recoiler Area
- Necessary Solenoid Valves and Controls at Control Console
ELECTRICAL
All electrical controls will be Allen Bradley with Eurotherm DC SCR drives (unless otherwise specified). All drives to be regenerative for quick stopping.
A single enclosed main console or control center complete with appropriate operator station will be included, pre-wired and ready for installation.
The necessary control console will be mounted at the rear of the machine with volt/phase/cycle input as required.
HYDRAULICS
All hydraulics will be Vickers or equivalent.
All hydraulic units will have pressure gauges, relief valves, pressure control, necessary filters, heat exchangers, and pressure shut off sensors where necessary.
Control will be at the control console, which will be located on the machine or the auxiliary equipment.
SAFETY
All necessary E-stop pushbuttons where required will be provided. Lockout/Tagout devices will also be provided. The customer is responsible for all safety aspects of the machinery, including all guarding and training of operators and maintenance personnel.