56´´ WIDE HOT STRIP MILL (USED)
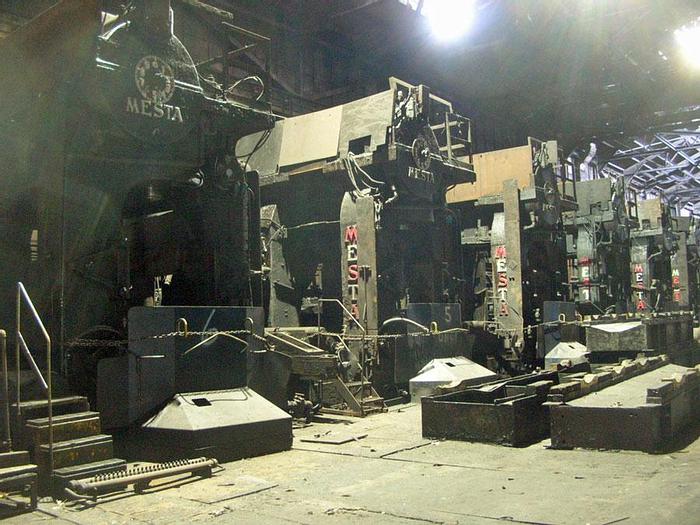
Specifications
Condition | Used |
Stock Number | VX-17360 |
Nominal capacity | 2,300,000 TPY |
Maximum undelayed rate | 350 TPH |
Piw | 575 |
Products | Low Carbon, High Carbon, HSLA, Scalp |
Slab size maximum | 9.45" x 52" x 216" (15 Tons) |
Coil width maximum | 52" |
Coil o.d. maximum | 60" |
Coil i.d. maximum | 30" |
Coil weight capacity maximum | 30,000 Lbs |
Finished gauges (nominal) | 0.5" to 0.056" in widths 20" to 51" |
Descale pressure | 2000 psi, 1964 |
Descale stations | 4 |
Vertical edger | Dominion Engineering, 1957 |
Four | Hi Reversing Mill |
Coil box | Stelco / Mesta, 1980 |
Crop shear | Dominion Engineering |
Scale breaker | Mesta, 1945 |
Thickness gauges | (2) DMC IGGI Sentinal 500, 1986 |
Laminar cooling | (4) Banks, 14,000 usg per min (Maximum) |
Downcoilers/upenders | (2) Dominion Engineering, 1964 |
Weigh scales | Systems Association Inc. 7000 (Rebuilt 1995) |
Cooling conveyor / downender | Eye Vertical Javis B. Webb pallet style, 1964 |
Banding / marking | Manual |
Description
Furnaces: 5 - Furnaces. 3 Zone Pusher type Rolling temperatures up to 2350 Deg F. Coke oven gas, natural gas and oil fired No 1 Rust Furnace Co., 1940 (Rebuilt 1980) No 2 Rust Furnace Co., 1946 No 3 Rust Furnace Co., 1952 No 4 Salem Brosius, 1965 No 5 Salem Industries, 1972 Line Includes: 29" to 33" Diameter x 108" Rolls 1500 HP Single Motor Drive 110" Roughing Mill: Mesta, 1941 48" to 52" diameter x 108" Backups 35" to 39" diameter x 110" Work Rolls 5000 HP Single motor drive Operated @ 7200 HP RMS with active cooling Back Up Roll Chocks - 8 (ie: 2 Per Roll, Enough for 2 Top Rolls and 2 Bottom Rolls) Work Roll Chocks - 8 (ie: 2 Per Roll, Enough for 2 Top Rolls and 2 Bottom Rolls) 1-3/8 " cut capability @ 52" wide 275 HP / 550 HP 16" Diameter x 56" Wide 75 HP Roll Chocks - 8 (ie: 2 Per Roll Enough for 2 Top Rolls and 2 Bottom Rolls) 56" Finishing Stands: (6) Stands, Mesta, 1945 4 - HI Mills 47" Diameter x 55" Backups 23" Diameter x 58" Work Rolls Backup Roll Chocks - 48 (ie: 2 Per Roll, Enough for 12 Top Rolls and 12 Bottom Rolls) Work Roll Chocks - 44 (ie: 2 Per Roll, Enough for 11 Top Rolls and 11 Bottom Rolls) Stands 1 to 5 have 3500 HP single motor drives Stand 1 upgraded to 5000 HP, 1980 (Nameplate remains 3500 HP) Stand 2 upgraded with a 5000 HP Armature, 1970s (Nameplate remains 3500 HP) Stand 6 has a 3000 HP single motor drive Width Gauge: (1) Kelk Accuband - 5, 1988 Continuously profiling 1/2" Thick (Maximum) 2300 FPM (Maximum) 375 HP Mandrel 400 Ft long The original install dates for the mill are: 1941 for: Furnace 1 110" Roughing Mill 1945 for: 6 Stand Finisher There have been significant improvements to the mill and the controls through the years. Furnace Area: Furnaces 2 through 5 were built between 1946 and 1972. All of the controls for the furnace movement remain CP type control. In 1996 the Operator controls were replaced and consolidated to one pulpit. This was accomplished using a new computer scheduling system, new mill feedback devices and PLC interfaces to the existing CP controls. The furnace heating controls were also upgraded though the 1990s replacing the pneumatic controls with modern electronic controllers. New flame safety systems were installed in the late 1980s. Rougher Area: The Descale systems were upgraded to 2000 psi pumps in 1964. New operator controls for these systems were installed in 1996 implemented through PLC interface and new mill feedbacks. The Rougher Entry and Exit tables were re-powered in 1996 with new SCR base drives with a digital control on the front end. Their speed and direction are controlled automatically. In 1996 all new Operator controls were also included. The Rougher Side Guards were re-powered in 1996 with new SCR base drives with a digital control on the front end. New digital feedbacks were included and the cross shafts were removed. The system is fully position regulated. The Rougher Screw Downs were re-powered in 1996 with new SCR base drives with a digital control on the front end. The motors were increase in size to 100 HP per side. New digital feedbacks were included and the cross shafts were removed. The system is fully position regulated. The Edger Gap Adjust was re-powered in 1996 with new SCR base drives with a digital control on the front end. New digital feedbacks were included and the cross shafts were removed. The system is fully position regulated. Although the main motor supplies remain M-G set the field supplies for the Generators and the Main mill motors for the Rougher and Edger were replaced in 1996 with new SCR base drives with a digital control on the front end. New digital feedbacks and Speed regulated controls were included. In 1996 all new Operator controls were included with an automation system on mill set-up and operation. Under normal operation the operator is in control of the speed and direction of the mill. All other operations are automatic. The transfer table power supplies were replaced in 1980 with GE solid state SCR packages and control. In 1996 the operator interface to these packages was upgraded and automated through a PLC and Digital control and new interfaces. Finisher Entry Area: The Coil Box (CB) was installed in 1980. All controls for this are Solid state. The drives for the CB are SCR based. The CB PLC was upgraded in 1996. The CB can operate in a fully automated mode. A new monitoring and fault analysis system was installed in 1996. With the exception of monitoring, the CB operator controls remain from 1980. The Crop Shear was refurbished in 1980. The crop shear control was replaced in 1985 with Solid state GE control. The MG set remains as the main supply. In 1996 all new Operator controls were included with an automation system. This interfaced into the existing 1985 controls using digital controllers and PLC control. The Scale Breaker generator and motor field supply and control were replaced in 1980 with Solid state GE control. The MG set remains as the main supply. In 1996 all new Operator controls were included with an automation system. This interfaced into the existing 1985 controls using digital controllers and PLC control. Finisher Area: The Finishing Mill (FM) has an original common bus power supply fed by four 3500 kW DC generators. Stands 3 through 6 main mill motors are original. They have been well maintained. In the 1970s Stand 2 armature was replace with a new 5000 HP unit. In 1980 Stand 1 motor (Armature and Field frame) was replace by a 5000 HP unit. The nameplates on these motors remain at 3500 Hp. In 1980 the Voltage control for the bus was changed to GE solid state. In 1980 a solid state Water Cooled SCR power supply was added to bus increasing the available power by more than 10,000 kW. In 1994 the Side Guard motors and control were changed to AC with VF drive control through a PLC. New position feedbacks were installed and a new position regulation and setup control was installed. In 1987 a new Kelk stereoscopic width gauge was installed. In 1998 the X-Ray gauges were rebuilt. In 1996 the following was replaced or added: All new Operator controls in a new pulpit An automation system including automated Mill Set-up. The new system consisted of Computer based set-up and digital operator screens. PLCs for the digital setup and control and a Digital Controller system for the regulators and drive controllers. The mill sets automatically after an operator command. There is a feed forward model to adjust the setup bar to bar. A new auto level on setup system was included. New Screw Down Drives and motors for Stands 3 through 6 increasing the HP by 50%. New Screw Down Position Regulation and Feedback with a split East West control. New Auto Gauge (BISRA) controls on Stands 1, 3 and 5. A width and X-Ray feedback loop is also incorporated. New force measurement feedback on all stands. New field packages for the Main Mill motors New speed feedbacks and regulation system for the Main Mill motors. New Armature and field packages, regulators, feedbacks and controls for the Loopers. New mill floor displays and controls. New radio control for the mill equipment (Screws and Side Guards) All new operator controls and new PLC system for the laminar flow models and loop controllers. This mill is operated tight with the loops down. The loopers are only used if there is slack between stands. The control loops for the loopers to operate in a regulation mode were added in 1996. The mill is not operated in this way because of the mechanics of the loopers and the common bus control. A new computer and PLC based mill monitor and annunciation system was added in 1996. This includes the drive systems and the Oil Cellar systems. A full logging system was implemented in 1996 following most mill parameters recording any change by the operator or the system logging the date time and the amount of change on the equipment from the furnace to the Laminar Sprays. Down Coiler Area: The Down Coilers were replaced in 1964. For the most part the controls remain the same from that time.