Melt Shop (100 Tons), Rolling Mills (800,000 TPY) Mesh Welding Line (Used)
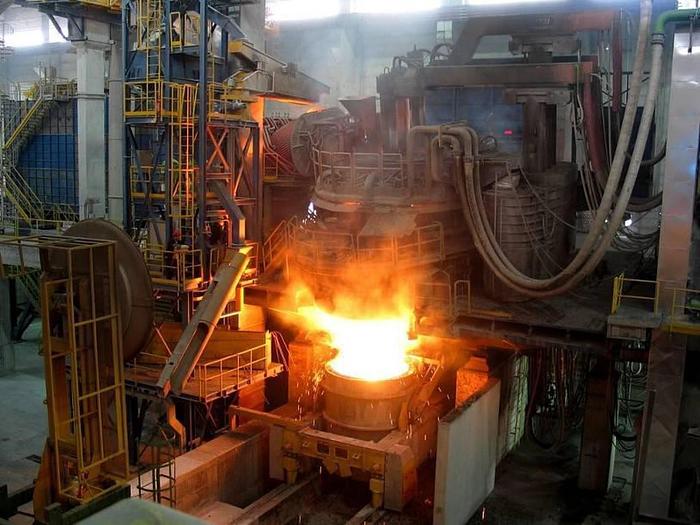
Specifications
Condition | Used |
Stock Number | VX-31034 |
Description
Plants & Starting Dates of Operation:
Melt Shop: February 2004
Rolling Mill 1: November 2003
Rolling Mill 2: November 2006
Mesh Welding 1: September 2003
Mesh Welding 2: July 2005
Mesh Welding 3: September 2006
Melt Shop – Highlights of the Plant:
Electric Arc Furnace:
100 t tapped steel, full platform, split shell, water cooled panels, EBT, conductive arms, electrodes
diameter 600mm, 72 MVA transformer, 3 oxygen modules , 3 burners carbon injection, 105 tph productivity,
annual production 609.000 tpy.
Ladle Furnace:
Active power 12 MW max., 350 mm electrode diameter.
Continuous Casting Machine:
4 strands, 7m radius, hot tundish, mould 1000mm length parabolic conic, billet size from100x100 mm to 160x160 mm, max billet length 12 m, casting speed 3,0 -3,8 m/min, productivity up to 108 tph, annual
production 600.000 tpy.
Fume Dedusting Plant:
Canopy hood, bag filter with 2 fans 450.000 m3/h each, dust collecting system.
Water Treatment Plant:
Contact and non-contact cooling circuits with cooling tower. Supplier DANIELI.
Cranes:
2X90t and 2x150t.
Scrap Handling:
2 transfer cars for scrap bucket handling.
Rolling Mill 1 – Main Characteristics:
Rolling Mill Nominal Capacity 500.000 tpy
Starting Material Billets 130x130 mm and/or 140x140 mm
Final Products:
Rounds/Deformed bars 8 – 40 mm diameter
Angles 25x3 – 50x5 mm
Channels 30x15 – 50x25 mm
Flats 30x5 – 80x30 mm
Squares 10x40 mm
Equal tees 25 -40 mm
Wire rod 5,5 – 16,0 mm
Deformed bars 8 – 20 mm diameter in
Spools Supplier: Danieli spa
Rolling Mill 1 – Mill Configuration and Composition:
115 tph Walking Hearth Reheating Furnace
Welding machine for endless rolling
Eighteen (18) H and V alternatively arranged rolling stands, being stands
16 and 18 Convertible (H/V) type to allow the slitting sequence of smaller
bar sizes and the twist free rolling of one-strand rolled products
Finishing facilities for bars, sections and coils
Lubrication/hydraulic services for the above
Water treatment plant
Electrical and level1,5 automation
Four slitting for 8 and 10 mm diameter
Reheating Walking Hearth Furnace:
Type: Walking hearth, top fired, lateral and frontal burners
Nominal Output: 115 tph
Fuel: Natural Gas
Supplier: Centro Combustion
Roughing Mill:
No of Stands: six (6) cantilever type Ring Diameter: 680 and 580 mm Ring Changing: In line by crane
Intermediate Mill:
No of Stands: six (6) housingless stands
Roll diameter: 440 mm
Stand changing: off-line with quick changing table
Finishing Mill:
No of Stands: six (6) housingless stands
Roll diameter: 370 mm
Stand changing: off-line with quick changing table
Shears:
Snap Shear: at roughing mill entry side
Crop Shear: at roughing mill exit side
Crop Shear: at intermediate mill exit side
Dividing Shear: at cooling bed entry side
Loopers:
Eight (8) vertical loopers before the intermediate and finishing stands
Water Cooling Line:
Two (2) water box chambers for surface quenching and bar cooling
Product to be cooled: 8 - 40 mm
Overall length: 21,5 m
Cooling Bed:
Bar cooling and transfer. Overall length: 78 m Overall width: 10,5 m
Multistrand Straightener:
Layer of sections straightening
Pendulum Shear:
Continuous cutting to length Head and tail cropping
Bar Counter:
Counting of bars for exact number of bars bundle forming
Single Head Magnetic Stacker:
Picking up the far layer and stack forming
Overall length: 12 m
Wire Binding Machines:
Wire binding of bar bundles and section stacks
Rolling Mill 2 – Main Characteristics:
Rolling Mill Nominal Capacity 300.000 tpy
Starting Material Billets 130x130 mm and/or 140x140 mm
Final Products:
Rounds/Deformed bars 8 – 20 mm diameter
Wire rod 5,5 – 16,0 mm in Coils
Deformed bars 8 – 20 mm diameter in
Spools Supplier: Danieli spa
Rolling Mill 2 – Mill Configuration and Composition:
80 tph Walking Hearth Reheating Furnace
Sixteen (16) H and V alternatively arranged rolling stands
Finishing block with six (6) mandrel units
Finishing facilities for bars and coils
Lubrication/hydraulic services for the above
Water treatment plant
Electrical and level1,5 automation
Reheating Walking Hearth Furnace:
Type: Walking hearth, top fired, lateral and frontal burners
Nominal Output: 80 tph
Fuel: Natural Gas
Supplier: Centro Combustion
Roughing Mill:
No of Stands: six (6) cantilever type Ring Diameter: 680 and 580 mm Ring Changing: In line by crane
Intermediate Mill:
No of Stands: six (6) cantilever type
Ring Diameter: 450 mm
Ring Changing: In line by crane
Finishing Mill:
No of Stands: four (4) housingless stands
Roll diameter: 370 mm
Stand changing: off-line with quick changing table
Shears:
Snap Shear: at roughing mill entry side
Crop Shear: at roughing mill exit side
Crop Shear: at intermediate mill exit side
Crop Shear: at fast finishing block entry side
Scrapping Shear: at the entry side of Dividing Shear
Dividing Shear: at cooling
bed entry side
Loopers:
Eight (8) vertical loopers before the intermediate and finishing stands
Water Cooling Line:
Water box chambers for surface quenching and bar cooling
Product to be cooled: 8 - 20 mm Overall length: 15.7 m
Pinch rolls:
To withdraw the rolled stock
Cooling Bed:
Bar cooling and transfer. Overall length: 78 m Overall width: 8,5 m
Cut to Length Shear:
Cutting to length Head and tail cropping
Bar Counter:
Counting of bars for exact number of bars bundle forming
Wire Binding Machines:
Wire binding of bar bundles
Rolling Mill 1+2 – WIRE ROD AREA:
Intermediate water cooling line
Pinch roll
Crop shear
Vertical looper
Finishing block with ten (10) mandrel units
Water cooling line with total overall length 35 m approx.
Four (4) pinch rolls
Laying head
Roller cooling conveyor, overall length 85 m
Coil forming station
Reel conveying roller table
Vertical coil compactor
Collecting saddles car
Sund Birsta Tying Machine
Rolling Mill 1+2 – SPOOLER LINE (double):
Diverter
Water cooling line
Pinch roll and Chopping Shear
Pinch roll and Vertical looper
Ring distributor and drum
Manipulator
Sund Birsta Tying Machines
Coil extraction
Roller table and coil evacuation
Mesh Welding Line 1:
Machine Type: EVG ATT 12/126-RV
Production of column and standard reinforcing mesh styles with line wire spacings
of 100, 125,150 and 200 mm.
Machine works with line and cross wires off spools (cold rolled ribbed wire) and mill coils
(hot rolled ribbed wire).
Production Data:
Max. width of mesh: 3.000 mm
Max. welding width: 2.900 mm
Max. length of mesh: 5.000 mm
Line wire diameter: 4 - 12 mm
Line wire spacing: 100, 125, 150 and 200 mm
Max. number of line wires: 30
Cross wire diameter: 4 - 8 mm
Cross wire spacing: min. 50 mm
Max. production speed: 125 cross wires/min
Mesh Welding Line 2:
Machine Type: EVG G95/126-RV
Production of column, special and standard reinforcing mesh styles with line wire spacing of
100, 125 and 150 mm.
Machine works with line from bars and with cross wires off mill coils (hot rolled ribbed or plain wire).
Production Data:
Max. width of mesh: 3.000 mm
Min. width of mesh: 1.200 mm
Max. welding width: 2.900 mm
Max. length of mesh: 6.000 mm
Line wire diameter: 6 - 12 mm
Line wire spacing: 100, 125, and 150
Max. number of line wires: 30
Cross wire diameter: 6 - 12 mm
Cross wire spacing: min. 50 mm
Max. production speed: 150 cross wires/min
Mesh Welding Line 3:
Machine Type: EVG G95/126-RV
Production of column, special and standard reinforcing mesh styles with line wire spacing of
100, 125 and 150 mm.
Machine works with line from bars and with cross wires off mill coils (hot rolled ribbed or plain wire).
Production Data:
Max. width of mesh: 3.000 mm
Min. width of mesh: 1.200 mm
Max. welding width: 2.900 mm
Max. length of mesh: 7.000 mm
Line wire diameter: 6 - 14 mm
Line wire spacing: 100, 125, and 150
Max. number of line wires: 30
Cross wire diameter: 6 - 12 mm
Cross wire spacing: min. 50 mm
Max. production speed: 150 cross wires/min